Second is the temperature range. Thermal pads need to be able to function properly within a specific temperature range. Different applications may have different operating temperature requirements, so it is necessary to choose a thermally conductive silicone pad that meets the required temperature range.
Compressibility and elasticity are also factors to consider. Thermally conductive silicone pad usually need to be compressed and deformed during device assembly to ensure good contact with heat sinks and heat sinks. Therefore, the compressibility and elasticity of thermal pads are very important, they should be able to return to their original shape under pressure and maintain good contact.
Chemical resistance is also a factor to consider. Thermally conductive silicone pad may need to come into contact with other chemicals such as oils, solvents, etc. Therefore, choosing a Thermally conductive silicone pad with good chemical resistance can ensure its stability and long-term service life in different environments.
The last is machinability. Thermally conductive silicone pads need to be able to be easily cut, shaped and customized to meet the needs of different equipment. Therefore, choosing a thermally conductive silicone pad that is easy to process can improve production efficiency and flexibility.
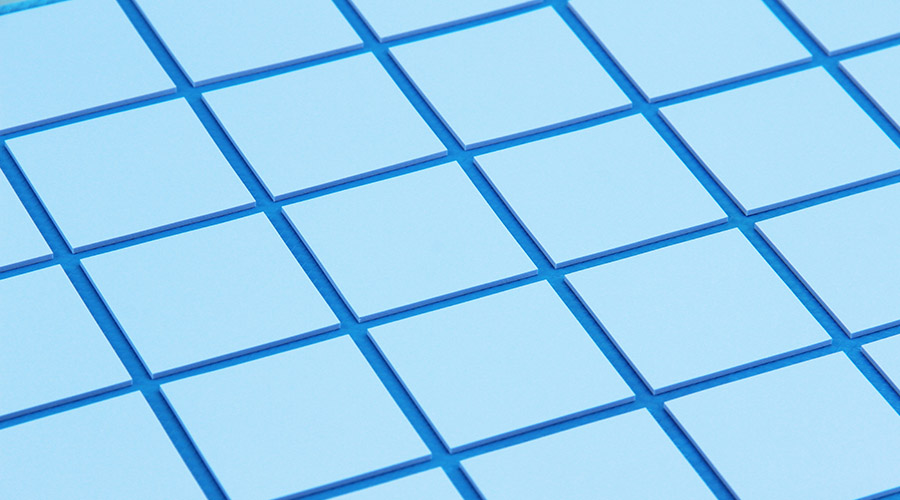